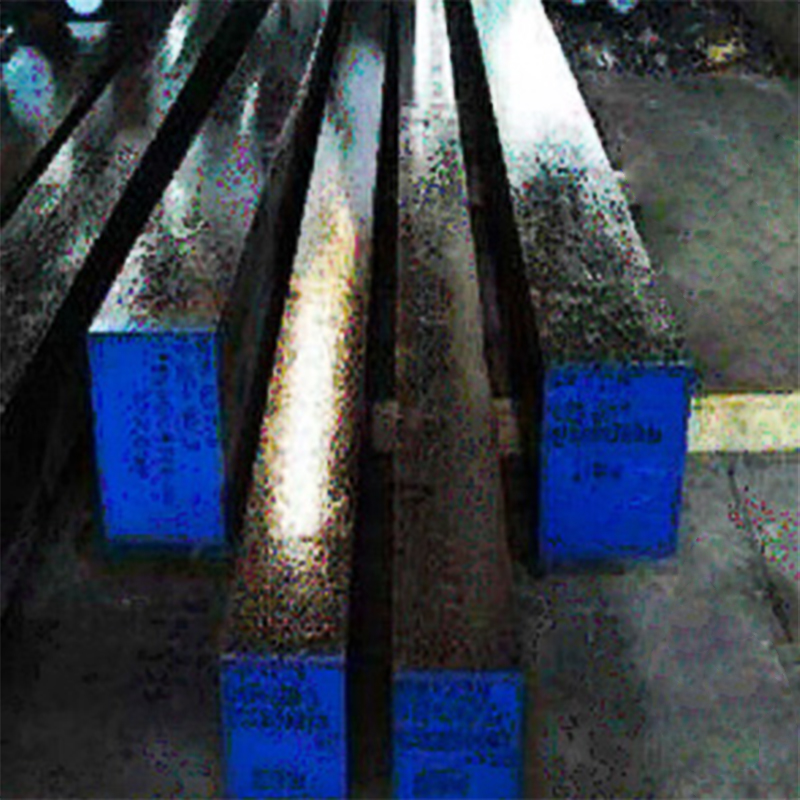
Качество поверхности легированной стали существенно изменяется после азотирования из-за образования на поверхности твердого износостойкого слоя. Вот ключевые изменения и характеристики отделки поверхности после азотирования:
Улучшенная износостойкость: образование твердого азотированного слоя на поверхности стали значительно повышает ее износостойкость. Этот слой действует как защитный барьер от механического износа, уменьшая потери материала при фрикционном контакте. Повышенная износостойкость азотированного слоя особенно полезна для компонентов, работающих в средах с высоким износом, таких как подшипники, детали клапанов и экструзионные шнеки. Азотированная поверхность снижает частоту технического обслуживания и замены, что приводит к снижению эксплуатационных затрат и повышению эффективности оборудования.
Шероховатость поверхности: Азотирование может вызвать небольшое увеличение шероховатости поверхности из-за образования нитридов. Начальная обработка поверхности легированной стали играет важную роль в определении конечной шероховатости после азотирования. Тщательно обработанные или полированные поверхности имеют тенденцию сохранять более гладкую поверхность, в то время как более шероховатые поверхности могут иметь более заметное увеличение шероховатости. Это изменение шероховатости можно свести к минимуму, контролируя параметры процесса азотирования и используя методы финишной обработки после азотирования, такие как полировка или шлифование, для достижения желаемой текстуры поверхности. Поддержание гладкой поверхности имеет решающее значение для применений, где требуется низкое трение и высокая точность.
Изменение цвета: Поверхность азотированной легированной стали обычно меняет цвет от темно-серого до черного. Это изменение цвета является результатом образования нитридов железа на поверхности. Затемненная поверхность является визуальным индикатором успешного процесса азотирования, а также может обеспечить некоторую степень коррозионной стойкости. Равномерное изменение цвета повышает эстетическую привлекательность детали и служит маркером контроля качества для последовательного азотирования в разных партиях.
Структура поверхности: Азотирование создает сложную структуру поверхности, характеризующуюся образованием составного слоя, также известного как белый слой, на верхней поверхности. Этот составной слой состоит из нитридов железа, в первую очередь ε-Fe2-3N и γ'-Fe4N, которые способствуют повышению твердости и износостойкости. Под слоем компаунда находится диффузионная зона, где атомы азота проникают в стальную матрицу, улучшая ее механические свойства. Слой компаунда обычно очень тонкий (несколько микрометров), но играет решающую роль в защите основного материала от износа и усталости. Такое структурированное наслоение повышает общую производительность и долговечность компонента.
Коррозионная стойкость: процесс азотирования может повысить коррозионную стойкость легированной стали за счет образования защитного слоя нитридов на поверхности. Эти нитриды действуют как барьер, предотвращая проникновение коррозионных агентов и снижая скорость окисления и образования ржавчины. Такое улучшение коррозионной стойкости особенно полезно для компонентов, подвергающихся воздействию агрессивных сред, таких как оборудование для химической обработки, морское оборудование и автомобильные детали. Повышенная коррозионная стойкость продлевает срок службы компонентов и снижает потребность в частом обслуживании или нанесении защитных покрытий.
Целостность поверхности. Азотирование улучшает общую целостность поверхности легированной стали, создавая сжимающие остаточные напряжения в поверхностном слое. Эти сжимающие напряжения противодействуют растягивающим напряжениям, которые могут привести к зарождению и распространению трещин, тем самым повышая усталостную прочность детали. Улучшенная целостность поверхности гарантирует, что азотированные компоненты смогут выдерживать циклические нагрузки и продлевать срок службы в сложных условиях эксплуатации. Азотированный слой также обеспечивает лучшую устойчивость к ударам и термоциклированию, что делает его пригодным для динамических и высокотемпературных сред.
Квадратный стержень из нержавеющей стали