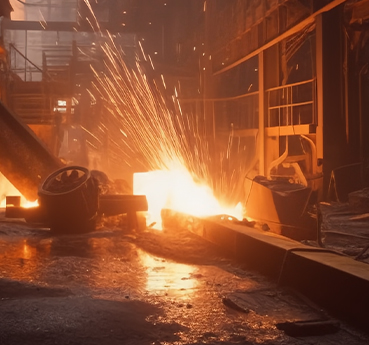
Ковка — это метод обработки, в котором используется ковочное оборудование для приложения давления к металлическим заготовкам, заставляя их подвергаться пластической деформации для получения поковок с определенными механическими свойствами, формой и размерами. Это один из двух основных компонентов ковки (ковки и штамповки). Ковка позволяет устранить такие дефекты, как пористость отливки в процессе выплавки металлов, оптимизировать микроструктуру, а благодаря сохранению полных линий потока металла механические свойства поковок обычно лучше, чем у отливок из того же материала. Важные детали в сопутствующих машинах с высокими нагрузками и тяжелыми условиями труда, за исключением простых профилей, которые можно раскатывать в листы, профили или сваривать, чаще всего изготавливают из поковок.
Температура деформации ковочных материалов
Начальная температура рекристаллизации стали делится на 800 ℃, при этом горячая ковка происходит выше 800 ℃; Ковка при температуре от 300 до 800 ℃ называется теплой или полугорячей ковкой, а ковка при комнатной температуре называется холодной ковкой. Поковки, используемые в большинстве отраслей промышленности, представляют собой горячую ковку, тогда как теплая и холодная ковка в основном используется для ковки деталей, таких как автомобили и общее оборудование. Теплая и холодная ковка позволяет эффективно экономить материалы.
Категория ковки
В зависимости от температуры ковки ее можно разделить на горячую ковку, теплую ковку и холодную ковку.
По механизму формования ковку можно разделить на свободную ковку, штамповку, кольцевую прокатку и специальную ковку.
1. Бесплатная ковка. Метод обработки ковки подразумевает использование простых универсальных инструментов или непосредственное приложение внешних сил между верхней и нижней наковальнями ковочного оборудования для деформации заготовки и получения необходимой геометрической формы и внутреннего качества. Поковки, изготовленные методом свободной ковки, называются свободными поковками. Свободная ковка в основном производит небольшие партии поковок с использованием ковочного оборудования, такого как молоты и гидравлические прессы, для придания формы и обработки заготовок и получения качественных поковок. Основные процессы свободной ковки включают высадку, удлинение, штамповку, резку, изгиб, скручивание, смещение и ковку. Свободная ковка использует метод горячей ковки.
2. Штамповка. Ковку в штампах можно разделить на ковку в открытых штампах и ковку в закрытых штампах. Металлические заготовки формуют путем деформации сжатия в камере ковочной матрицы определенной формы для получения поковок. Ковка обычно используется для изготовления деталей небольшого веса и больших партий.
Ковку в штампах можно разделить на горячую ковку, теплую ковку и холодную ковку. Теплая и холодная ковка являются будущими направлениями развития штамповки, а также представляют собой уровень технологии ковки. В соответствии с классификацией материалов ковку также можно разделить на ковку черного металла, ковку цветных металлов и формовку порошковых изделий. Как следует из названия, материалы представляют собой черные металлы, такие как углеродистая сталь, цветные металлы, такие как медь и алюминий, а также материалы порошковой металлургии. Экструзия должна относиться к штамповке и может быть разделена на экструзию тяжелых металлов и экструзию легких металлов. Следует отметить, что заготовку нельзя полностью ограничить. Поэтому необходимо строго контролировать объем заготовки, контролировать взаимное положение кузнечного штампа, измерять поковки, стремясь уменьшить износ ковочного штампа.
3. Шлифовальное кольцо. Кольцевая прокатка относится к производству круглых деталей различного диаметра с использованием специального оборудования, такого как кольцепрокатные станки, а также используется для производства деталей колесной формы, таких как колеса автомобилей и колеса поездов.
4. Специальная ковка. Специальная ковка включает в себя такие методы ковки, как валковая ковка, поперечно-клиновая прокатка, радиальная ковка и ковка в жидкой штамповке, каждый из которых больше подходит для изготовления определенных деталей специальной формы.
Например, валковая ковка может служить эффективным процессом предварительного формования, значительно снижая последующее давление формования; Поперечная клиновая прокатка позволяет производить такие детали, как стальные шарики и трансмиссионные валы; Радиальная ковка позволяет производить крупные поковки, такие как стволы орудий и ступенчатые валы.
ковочная матрица
В зависимости от режима движения ковочного штампа ковку можно разделить на качающуюся ковку, поворотную ротационную ковку, валковую ковку, поперечно-клиновую прокатку, кольцевую прокатку и косую прокатку. Роторная ковка, ротационная ковка и прецизионная ковка также могут быть использованы для тяжелого авиационного ковочного гидравлического пресс-кольца 400 МН (40 000 тонн) в Китае. Чтобы улучшить коэффициент использования материалов, в качестве предшествующих процессов обработки тонких материалов можно использовать валковую ковку и поперечную прокатку. Ротационную ковку, как и свободную ковку, также производят локально, и ее преимущество состоит в том, что ее можно формовать даже при меньших усилиях ковки по сравнению с размером поковки. Этот метод ковки, в том числе свободная ковка, предполагает расширение материалов от поверхности формы к свободной поверхности во время обработки, что затрудняет обеспечение точности. Таким образом, управляя направлением движения кузнечного штампа и процессом ротационной ковки с помощью компьютера, можно получать изделия сложной формы и высокой точности с меньшим усилием ковки, например, производство поковок с несколькими разновидностями и большими размерами лопаток паровых турбин. .
Движение формы и степени свободы ковочного оборудования несовместимы. По характеристикам ограничения деформации в нижней мертвой точке ковочное оборудование можно разделить на следующие четыре вида:
1. Форма ограниченной силы ковки: гидравлический пресс, который непосредственно приводит в движение ползунок под давлением масла.
2. Метод ограничения квазихода: гидравлический пресс, приводящий в движение кривошипно-шатунный механизм гидравлическим давлением.
3. Способ ограничения хода: механический пресс с кривошипом, шатуном и клиновым механизмом, приводящим в движение ползун.
4. Метод ограничения энергии: используйте спиральный механизм винта и фрикционный пресс. Для достижения высокой точности при горячих испытаниях тяжелых авиационных ковочных гидравлических прессов следует уделять внимание предотвращению перегрузок в нижней мертвой точке, контролю скорости и положения пресс-формы. Потому что это будет влиять на допуск, точность формы и срок службы поковок. Кроме того, для сохранения точности следует также уделить внимание регулировке зазора между направляющими ползунов, обеспечению жесткости, регулировке нижней мертвой точки, использованию вспомогательных передаточных устройств.
Кованый слайдер
Кузнечные ползуны можно разделить на вертикальные и горизонтальные перемещения (применяются для ковки тонких деталей, смазки, охлаждения, ковки высокоскоростных деталей), а для увеличения перемещения в других направлениях могут применяться компенсационные устройства. Вышеупомянутые методы различны, и сила ковки, процесс, коэффициент использования материала, производительность, допуск на размер, а также метод смазки и охлаждения, необходимые для успешной ковки продукта большого дискового типа, различны. Эти факторы также являются факторами, влияющими на уровень автоматизации.Материалы, используемые для ковки
Основными материалами, используемыми для ковки, являются углеродистая сталь и легированная сталь различного состава, затем следуют алюминий, магний, медь, титан и их сплавы. К исходному состоянию материалов относятся слитки, слитки, металлические порошки и жидкие металлы. Отношение площади поперечного сечения металла до деформации к площади поперечного сечения после деформации называется коэффициентом ковки. Правильный выбор коэффициента ковки, разумная температура нагрева и время изоляции, разумная начальная и конечная температура ковки, разумная величина деформации и скорость деформации тесно связаны с улучшением качества продукции и снижением затрат. Обычно в поковках малого и среднего размера в качестве заготовок используются круглые или квадратные прутки. Зернистая структура и механические свойства стержневого материала однородны и хороши, имеют точную форму и размер, хорошее качество поверхности и простоту организации массового производства. При разумном контроле температуры нагрева и условий деформации можно производить высокопроизводительные поковки без значительной деформации. Слитки используются только для крупных поковок. Слиток представляет собой отлитую структуру с крупными столбчатыми кристаллами и рыхлым центром. Поэтому необходимо разбивать столбчатые кристаллы на мелкие зерна посредством большой пластической деформации и рыхло уплотнять их для получения металлической структуры и механических свойств. Заготовки порошковой металлургии, изготовленные прессованием и обжигом, в горячем состоянии можно перековывать в порошковые поковки без заусенцев. Плотность ковочного порошка близка к плотности обычных поковок, имеет хорошие механические свойства и высокую точность, что позволяет сократить последующую обработку резанием. Внутренняя структура порошковых поковок однородна, без расслаивания, и ее можно использовать для изготовления небольших зубчатых колес и других деталей. Однако цена порошка значительно выше, чем у обычных брусков, а его применение в производстве имеет определенные ограничения. Прикладывая статическое давление к заливаемому в полость формы жидкому металлу, который затвердевает, кристаллизуется, течет, подвергается пластической деформации и формуется под давлением, можно получить необходимую форму и характеристики штамповки. Ковка жидкого металла — это метод формования, который находится между литьем под давлением и ковкой, особенно подходит для сложных тонкостенных деталей, которые трудно сформировать при обычной ковке. Помимо обычных материалов, таких как углеродистая сталь и легированная сталь различного состава, за которыми следуют алюминий, магний, медь, титан и их сплавы, деформационные сплавы из жаропрочных сплавов на основе железа, жаропрочных сплавов на основе никеля, Жаропрочные сплавы на основе кобальта также комплектуются ковкой или прокаткой. Однако эти сплавы имеют относительно узкие пластические зоны, поэтому сложность ковки сравнительно высока. Различные материалы предъявляют строгие требования к температуре нагрева, температуре открытой ковки и конечной температуре ковки.
Схема процесса ковки
Различные методы ковки имеют разные процессы, среди которых процесс горячей штамповки является самым продолжительным, а общий порядок таков: ковочная резка заготовок; Нагрев ковочной заготовки; Подготовка ковочной заготовки; штамповка штамповки; Режущие края; Штамповка; Коррекция; Промежуточный контроль, проверка размеров и поверхностных дефектов поковок; Термическая обработка поковок для устранения напряжений при штамповке и улучшения характеристик резания металла; Очистка, в основном для удаления поверхностного оксидного налета; Коррекция; Проверка: Как правило, поковки должны подвергаться проверке внешнего вида и твердости, в то время как важные поковки также должны подвергаться анализу химического состава, механических свойств, испытаниям на остаточное напряжение и неразрушающему контролю.
Характеристики поковок
По сравнению с литьем металл может улучшить свою микроструктуру и механические свойства после обработки ковкой. После горячей обработки и деформации методом ковки за счет деформации и рекристаллизации металла структура отливки превращается из крупных дендритов и столбчатых зерен в равноосные рекристаллизованные структуры с более мелкими и однородными размерами. Это вызывает в стальном слитке первоначальную сегрегацию, пористость, пористость, шлаковые включения и другие уплотнения и сварки, делая структуру более компактной и улучшая пластичность и механические свойства металла. Механические свойства отливок ниже, чем у поковок из того же материала. Кроме того, обработка ковкой может обеспечить непрерывность структуры металлического волокна, сохраняя структуру волокна поковки в соответствии с формой поковки. Линия подачи металла укомплектована, что гарантирует хорошие механические свойства деталей и длительный срок службы. Поковки, полученные методами точной ковки, холодной экструзии, теплой экструзии и других процессов, не сравнимы с отливками. Поковки — это объекты, которым придают форму путем пластической деформации, чтобы они соответствовали требуемой форме или подходящей силе сжатия, когда металл подвергается давлению. Эта мощность обычно достигается за счет использования молотка или давления. В процессе ковки создаются изысканные структуры частиц и улучшаются физические свойства металла. При практическом использовании компонентов правильная конструкция может гарантировать, что поток частиц будет направлен в направлении основного давления. Отливки — это металлические изделия, полученные различными методами литья, то есть расплавленный жидкий металл впрыскивается в заранее подготовленные формы посредством разливки, впрыска, всасывания или других методов литья, охлаждается, а затем подвергается удалению песка, очистке и последующей обработке. -обработка для получения объектов определенной формы, размера и эксплуатационных качеств.
Анализ уровня ковки
Китайская кузнечная промышленность развивалась на основе внедрения, освоения и освоения иностранных технологий. После многих лет технологического развития и трансформации технический уровень предприятий отрасли значительно улучшился, включая проектирование процессов, технологию ковки, технологию термообработки, технологию механической обработки, испытания продукции и другие аспекты.
(1) Передовые производители в проектировании процессов обычно применяют технологии компьютерного моделирования горячей обработки, автоматизированного проектирования процессов и виртуальные технологии, повышая уровень проектирования процессов и возможности производства продукции. Внедряйте и применяйте программы моделирования, такие как DATAFOR, GEMARC/AUTOFORGE, DEFORM, LARSTRAN/SHAPE и THERMOCAL, для обеспечения управления процессами компьютерного проектирования и термической обработки.
(2) Большинство гидравлических прессов с технологией ковки с усилием 40 МН и выше оснащены усилием 100-400 тонн. м главных кузнецов и 20-40т. m вспомогательных операторов. Значительное количество операторов используют компьютерное управление для комплексного контроля процесса ковки, позволяя контролировать точность ковки в пределах ± 3 мм. Для онлайн-измерения поковок используются лазерные устройства измерения размеров.
(3) Целью технологии термообработки является улучшение качества продукции, повышение эффективности термообработки, экономия энергии и защита окружающей среды. Если процесс нагрева нагревательной печи и печи для термообработки контролируется компьютером, горелкой можно управлять для автоматической регулировки горения, температуры печи, автоматического зажигания и управления параметрами нагрева; Утилизация отработанного тепла, печи термической обработки, оснащенные регенеративными камерами сгорания и т.д.; Благодаря использованию полимерных резервуаров для закалочного масла с низкой степенью загрязнения и эффективным контролем охлаждения различные закалочные среды на водной основе постепенно заменяют традиционное закалочное масло.
(4) Доля станков с ЧПУ в обрабатывающей промышленности постепенно увеличивается. Некоторые предприятия отрасли имеют обрабатывающие центры и оснащены собственным обрабатывающим оборудованием по различным видам изделий, например, пятикоординатными обрабатывающими центрами, лопастными станками, валковыми станками, токарно-карусельными станками и т. д.
(5) Меры по обеспечению качества: некоторые отечественные предприятия оснащены новейшими приборами обнаружения и технологиями тестирования, современными автоматизированными системами ультразвукового контроля с компьютерной обработкой данных и различными специализированными автоматическими системами ультразвукового контроля для завершения сертификации различных систем качества. Ключевая технология производства высокоскоростных сверхмощных зубчатых поковок постоянно отрабатывалась, и на этой основе было достигнуто промышленное производство. Благодаря внедрению передовых технологий производства и ключевого оборудования из-за границы, Китай смог самостоятельно спроектировать и изготовить производственное оборудование для высокоскоростной и сверхпрочной зубчатой поковки. Это оборудование приблизилось к международному передовому уровню, а улучшение технологий и уровня оборудования эффективно способствовало развитию отечественной кузнечного производства.
Важность ковки
Кузнечное производство является одним из основных способов обработки заготовок механических деталей в машиностроении. Путем ковки можно не только получить форму механических деталей, но и улучшить внутреннюю структуру металла, а также улучшить механические и физические свойства металла. Как правило, важные механические детали, подвергающиеся высоким нагрузкам и требованиям, изготавливаются с использованием методов ковки. Важные компоненты, такие как валы турбогенераторов, роторы, рабочие колеса, лопасти, стопорные кольца, большие колонны гидравлических прессов, цилиндры высокого давления, валки стальных прокатных станов, коленчатые валы двигателей внутреннего сгорания, шатуны, шестерни, подшипники и артиллерийские орудия в национальной обороне. промышленности все производятся посредством ковки. [7] Поэтому ковочное производство широко используется в таких отраслях, как металлургия, горнодобывающая промышленность, автомобили, тракторы, лесозаготовительная техника, нефтяная, химическая промышленность, авиация, аэрокосмическая промышленность, вооружение и т. д. Даже в повседневной жизни ковочное производство также играет важную роль. . В некотором смысле годовой выпуск поковок, доля штампованных поковок в общем объеме производства поковок, а также размер и принадлежность ковочного оборудования в определенной степени отражают промышленный уровень страны